Wave-Box: Der fünfte Magen der Kuh
In der Biogasanlage der Anklamer Agrar AG wird Ultraschall zur Effizienzsteigerung eingesetzt. Wir haben uns das System erklären lassen und nachgefragt, ob der Betreiber damit zufrieden ist.
Eine Kuh hat bekanntlich vier Mägen. Trotzdem verwertet sie nicht alles, und aus ihrer Hinterlassenschaft lässt sich noch ordentlich Energie gewinnen, wenn man sie beispielsweise in eine Biogasanlage gibt. Doch auch die hungrigsten Mikroorganismen in dem Fermenter schaffen es nicht, jede organische Bindung zu knacken und in Methangas umzuwandeln. Und hier kommt die Wave-Box ins Spiel, oder wie Norbert Rossow sagt: „der fünfte Magen der Kuh“.
Der Neue-Energien-Spezialist ist Geschäftsführer der PRE Power Recycling Energyservice GmbH aus Neubrandenburg. Das Unternehmen plant und steuert unter anderem den Bau von Biogasanlagen, beschäftigt sich mit der Biogasreinigung, -aufbereitung und -nutzung sowie der Effizienzsteigerung dieser Anlagen. Für Letzteres hat Norbert Rossow gemeinsam mit seinem Team die Wave-Box entwickelt. Das ist ein nicht weiter auffälliger, kleiner grauer Container, der neben dem Fermenter steht und in dessen Innerem Schwerverdauliches mithilfe von Ultraschall doch noch aufgeschlossen wird. Wie das genau passiert, erklärte uns Geschäftsführer Rossow:
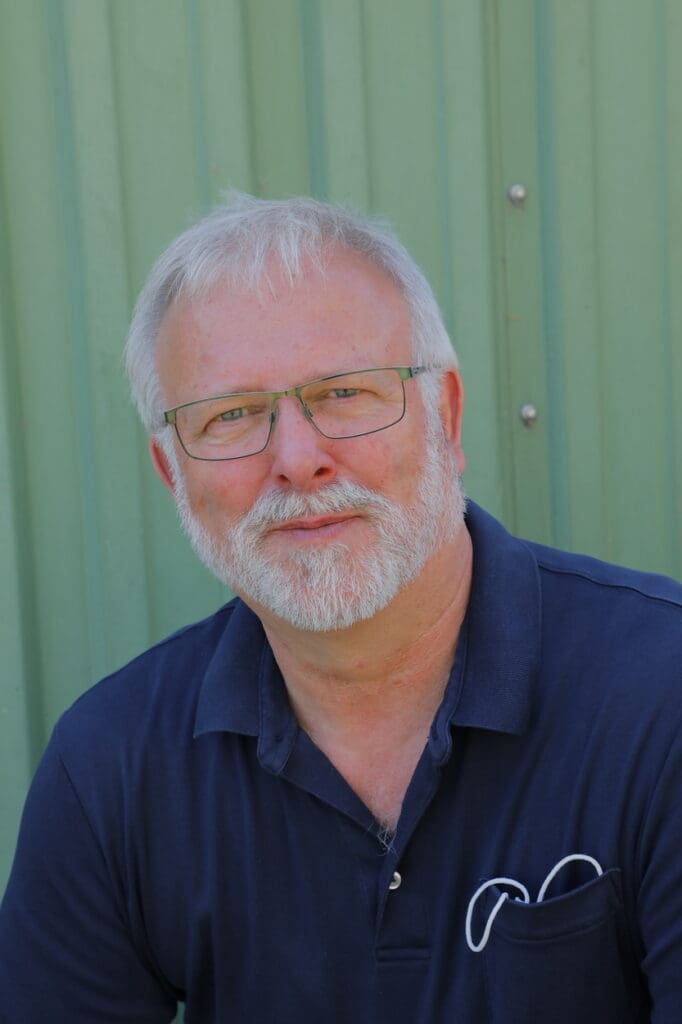
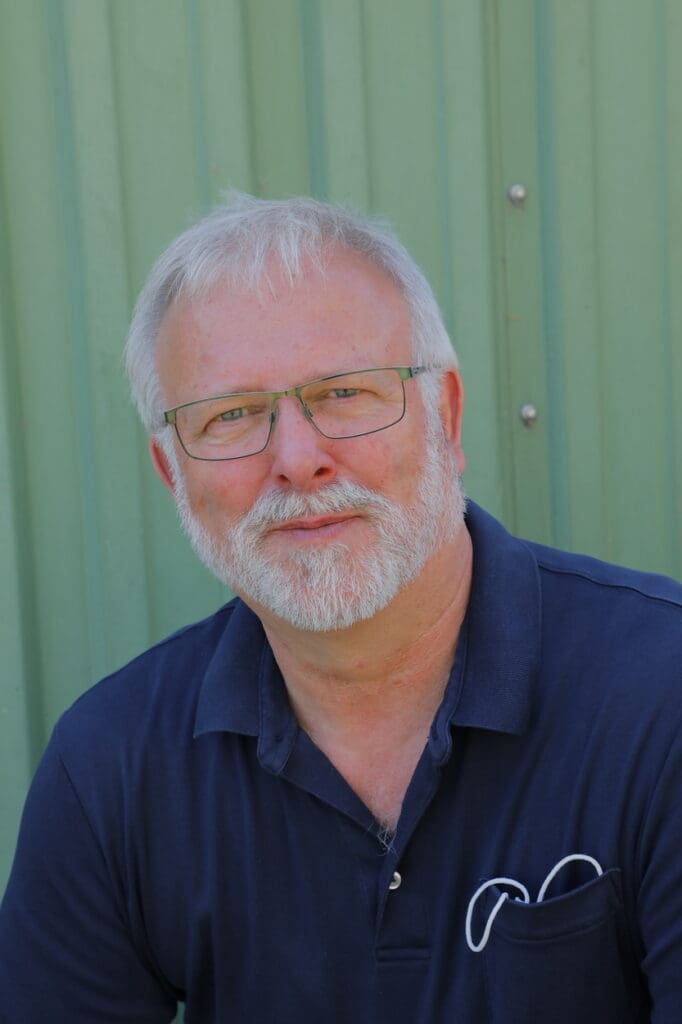
Jenseits des Hörschalls
Das wesentliche Bauteil der Box ist ein Hochleistungs-Ultraschallsystem. Zudem gibt es ein Messgerät für den Volumendurchfluss, eine druck- und volumengeregelte Pumpe, Sensoren und Spülleitungen sowie eine sich selbst optimierende und -überwachende Steuereinheit. Die Ultraschallreaktoren, auch Sonotroden genannt, arbeiten im Durchlaufsystem mit hoher Intensität.
Als Ultraschall bezeichnet man Schall in Frequenzen jenseits des Hörschalls, also von 20 kHz bis in den Megaherzbereich. Beschallt man damit ein wässriges Medium, werden in ihm periodisch und rasend schnell Druck und Unterdruck erzeugt. Beim Unterdruck kommt es zum Aufreißen der Wasserphase, was zur Bildung von mikroskopisch kleinen Hohlräumen in der Flüssigkeit führt. Diese Bläschen füllen sich mit Wasserdampf oder Gas. Sie wachsen in den Zugphasen und schrumpfen in den Druckphasen, bis sie in sich zusammenbrechen. Dieser Vorgang wird als Blasen implosion bezeichnet und setzt im Mikromaßstab enorme Drücke von bis zu 500 bar frei. Solche Kräfte sind in der Lage, jede noch so robuste Oberfläche zu zerstören. Gelangt nun Biomasse in den Wirkbereich der Ultraschallwellen, werden die in ihr enthaltenen organische Zellverbände zerstört, die Gesamtoberfläche des Gärsubstrates vergrößert sich. Wird das Substrat weiter beschallt, öffnen sich anschließend die Pflanzen- und Bakterienzellen, Fasern werden zerrissen und Zellinhaltsstoffe freigesetzt. Damit werden bislang eingeschlossene Nähr- und Mikronährstoffe freigesetzt, auf die sich die aktiven Mikroorganismen stürzen, wenn das beschallte Substrat in den Fermenter zurückgepumpt wird. Denn je mehr chemische Verbindungen aufgeschlossen werden, umso höher ist der Grad der Fermentierung. Zusätzlich unterstützen freigesetzte Enzyme den gesamten Abbauprozess. Mehr Biogas ist die Folge.
„Die Wave-Box ist ein patentiertes Hochleistungs-Ultraschallsystem, das optimal auf die Desintegration von stark faserhaltiger Biomasse abgestimmt ist“, fasst Norbert Rossow seine Entwicklung zusammen. „Die fasereichen Bestandteile im Substrat werden aufgelöst und die Hydrolyse effizienter.“ So könnten 10 bis 20 % mehr Biogas aus dem Gärsubstrat gebildet werden, wobei der Mehrertrag die eingesetzte Energie um den Faktor 12 bis 15 übertreffe.
Dass er mit diesen Aussagen nicht falschliegt, kann Karsten Schmoock beweisen. Der Leiter Wissenschaft und Entwicklung im Ingenieurbüro PRE ist studierter Lebensmittel- und Bioprodukttechnologe und hat an seiner ehemaligen Fachhochschule in Neubrandenburg auch noch einen Lehrauftrag. Er betreut die Erst- und Zweitsemester im Fachbereich Agrarwissenschaften bei ihren Chemiepraktika. „Ich nehme Proben vom Gärsubstraten vor und nach der Ultraschallbehandlung und untersuche sie in unserem Firmenlabor“, erklärt der 33-Jährige. Was ihn dabei besonders interessiert, ist der CSB. Das ist die Abkürzung für chemischer Sauerstoffbedarf, einen Summenparameter, der verrät, wie viele biologisch abbaubare Stoffe in einer Flüssigkeit vorhanden sind. Steigt der gelöste CSB-Anteil nach der Beschallung, weist das den Erfolg der Substratbehandlung nach. Die größten CSB-Steigerungen durch Ultraschall kann er bei Anlagen nachweisen, die nur auf Rindergülle setzen. „Der Ultraschall knackt die Zellulose- und Hemizelluloseverbindungen, die für den Rindermagen unverdaulich und auch in der Biogasanlage nur schwer abbaubar sind“, erklärt der gebürtige Neubrandenburger.
„Die Anlagenbetreiber müssen sich aber nicht nur auf unsere Analysen verlassen“, ergänzt PRE-Chef Rossow und zeigt uns das Gutachten eines akkreditieren Prüflabors in Altenberge (NRW). Zudem könne er beispielsweise auf die Biogasanlage Sandhagen bei Friedland verweisen. Dort hätten sie Leistungssteigerungen von 15 bis 18 % erzielt. Bei Anlagen, die nur Mais vergären, wären Steigerungen von 8 bis 12 % möglich.
g
Fünf Tonnen Maissilage
Eine Leistungssteigerung war für die Anklamer Agrar AG aber nicht der Grund, warum sie ihr Gärsubstrat ultrabeschallt. „Wir sparen dadurch bis zu fünf Tonnen Maissilage pro Tag“ bringt es Anlagenfahrer Maik Krüger auf den Punkt.
Er betreut die 600-kW-Anlage am Standort Woserow im Landkreis Vorpommern-Greifswald seit ihrer Inbetriebnahme 2011. Sie besteht aus einem 4.000-m3-Fermenter, einem 5.000-m3-Endlager und einer Hydrolyse, die 215 m3 fasst. Im Fermenter drehen sich drei Langwellenrührwerke. Das Hauptsubstrat ist die Gülle von 1.300 Milchkühen. Dazu kommen täglich rund 6 t Festmist, den die Milchviehnachzucht erzeugt. Zusätzlich schütten sie circa 6 t Mais- und/oder Grassilage in den Fliegl-Feststoffdosierer. Mit der BHKW-Abwärme trocknen sie ihre Gärreste, um Lagerkapazität einzusparen. Den Biogasstrom speisen sie in das Netz der Eon Edis ein. Das macht auch die benachbarte 530-kW-Biogasanlage der Bioenergie Anklam GmbH. Sie wird ebenfalls von Maik Krüger und seinen Kollegen mit Rindergülle und Silage versorgt. Ihre BHKW-Abwärme beheizt Sozialgebäude sowie Werkstatt der Milchviehanlage und bereitet Warmwasser.
Wartungsfrei und autark
Mit der Wave-Box zeigt sich Anlagenfahrer Krüger zufrieden. Sie arbeite wartungsfrei und autark. Das heißt, würde sie ausfallen, stört das nicht die Biogaserzeugung. Sie kann von ihm über die Karsten Schmoock nimmt regelmäßig und routiniert „anrüchige“ Substratproben. Da staunen sicher auch die Kühe. Steuereinheit, aber auch direkt übers Internet von den Neubrandenburger Ingenieuren überwacht und geregelt werden. Ihre Installation hat nur zwei Tage gedauert. Anfangs habe es allerdings Probleme gegeben, weil der Techniklieferant versehentlich eine falsche Pumpe eingebaut hatte. Aber seitdem das korrigiert wurde, wirke sich die Substratbeschallung spürbar auf die Menge der Einsatzstoffe aus – und auf die der Gärprodukte. Die festen Rückstände würden nämlich deutlich weniger, wenn viele der bislang ungenutzten Fasern nun in Biogas umgewandelt werden. „Gerade wenn man die Futtersituation der letzten beiden Dürrejahre bedenkt, sind wir froh, dass wir jetzt weniger Maissilage für das Biogas einsetzen müssen“, berichtet der Landwirt. „Ganz abgesehen von der Kostensenkung.“
Vielfache Wirkungen
Das Stichwort „Kosten“ nimmt dann Norbert Rossow wieder auf, und erklärt, dass sich die Anschaffungs- und Betriebskosten für die Ultraschalltechnik – je nach Art der Einsatzstoffe – nach zwei bis fünf Jahren amortisieren würden. „Es kann aber auch noch deutlich schneller gehen, wie das Beispiel Sandhagen zeigt“, gibt er zu bedenken. Nur 3 bis 5 kW Energieeinsatz würden bei einer 500- bis 600-kW-Anlage rund 75 kW mehr Strom erzeugen. Zudem verdopple sich die Pumpleistung beim Ausbringen der Gärprodukte – in Anklam wird Gülleverschlauchung praktiziert. Nicht zu vergessen sei die ökologische Entlastung durch einen geringeren Nachgärprozess von 15 bis 18 % Ammoniakäquivalent. Der beschleunigte Abbau der Organik führe zu weniger Restmethanbildung und senke die erforderliche hydraulische Verweilzeit. Dann verweist der Biogasfachmann noch darauf, dass der Ultraschall die für die Schaumbildung im Fermenter verantwortlichen Mikroorganismen zerstöre. Da er aber auch die Methangasbildner abtötet, wird das Substrat aus dem unteren Bereich des Fermenters genutzt, wo sich nur relativ wenige von ihnen aufhalten.
Der nicht weiter auffällige, kleine graue Container ist aber offensichtlich nicht das Ende der Fahnenstange. Sein Unternehmen arbeitet gemeinsam mit dem Leibniz-Institut für Plasmaforschung und Technologie in Greifswald sowie der Universität Rostock bereits seit drei Jahren an einer Weiterentwicklung. Dabei ist es ihnen gelungen, Plasma in flüssigen Medien zu zünden und stabil zu halten. Ihre Ultraschall-Plasma-Kombination schaffe es, noch mehr Agglomerate aufzubrechen. Die Methangaserzeugung würde um weitere 25 % und der schon erwähnte, gelöste CSB überproportional ansteigen. – Das aber ist dann schon wieder eine neue Reportage.